INTRODUÇÃO
O Fabricante de Rações tem como objetivo produzir rações com a melhor relação custo x benefício. Toda a gestão do processo de fabricação de ração deve estar voltada para atender o produto final com qualidade visando esta finalidade.
No Planejamento e Gestão do Processo de Fabricação com visão ao atendimento da qualidade de ração deve-se ter o processo que atenda a qualidade desejada. A qualidade pode ser planejada em novos projetos ou por meio da gestão, através de um estudo da situação atual, adequando os desvios de qualidade para plantas existentes. O conhecimento tecnológico das etapas de processo dá o suporte para o planejamento e gestão.
Este trabalho esta divido em 3 partes e tem como objetivo sintetizar o conhecimento tecnológico e prático existente no processo de produção de ração, disponibilizando um referencial para projetos que envolvem as etapas de Moagem, Mistura e Peletização.
Ficando esta primeira parte abordando o tópico qualidade da ração, processo de fabricação (pré e pós moagem) e moagem. Na seqüência, Parte 2 - Mistura e na Parte 3 - Peletização.
QUALIDADE DA RAÇÃO
A qualidade intrínseca da ração divide-se em duas dimensões, qualidade nutricional/fisiológica e sanitária.
Nutricional/Fisiológica
Entende-se que a qualidade nutricional/fisiológica trata do atendimento dos níveis nutricionais para cada fase de vida do animal. Os níveis nutricionais são alcançados através da dosagem e pesagem adequada dos ingredientes individuais, e posterior mistura para uniforme homogeneização dos ingredientes.
Outro fator atendido por esta dimensão de qualidade é a granulometria adequada ao aparelho digestivo de cada espécie. Para os suínos é usada uma granulometria mais fina, e para as aves, em função de sua natureza, uma granulometria mais grossa.
A qualidade física do pelete é medida através de sua durabilidade e dureza. O pelete deve ser durável, mas não duro em demasia. De acordo com o autor Nir (1994) citado pelo Nir [11] , peletes duros (grau de peletização 2, dupla peletização) reduz os efeitos benéficos da peletização para aves.
Sanitária
A ração deve ser isenta de microorganismos, bem como não deve possuir nenhum componente tóxico ou componente indesejado que pode prejudicar a saúde do animal ou deixar resíduo indesejável na carne.
PROCESSO DE FABRICAÇÃO DE RAÇÃO
Uma das primeiras definições que deve ser levada em consideração no planejamento de uma fábrica de ração é a escolha do conceito de moagem que será adotado, a pré-moagem ou a pós-moagem.
A pré-moagem foi a maneira original que as fábricas de rações no Brasil foram montadas. Nesta, os ingredientes são moídos individualmente e posteriormente são dosados (Figura 1). Basicamente, são utilizados como ingredientes a serem moídos, o milho ou outro grão alternativo e o farelo de soja.
.
Figura 1. Fluxograma de uma fábrica de rações com pré-moagem Fonte: Buhler [4]A pós-moagem é uma nova tendência das novas fábricas e seu uso no Brasil teve início em meados dos anos 90, por influência do modelo europeu de produção de rações. A pós-moagem, também chamada moagem conjunta, coloca o sistema de moagem entre a dosagem e a mistura, dentro da linha de produção. Neste sistema, todos os ingredientes são armazenados diretamente nos silos de dosagem, já que a moagem é realizada na linha de produção. Este processo foi desenvolvido devido a necessidade no mercado europeu de produzir rações com uma grande variedade de ingredientes que necessitassem da moagem (Figura 2).
Figura 2. Fluxograma de uma fábrica de rações com pós-moagem Fonte: Buhler [4]
A vantagem da pré-moagem é o moinho ser independente da linha da mistura, e consequentemente a capacidade de moagem pode ser utilizada completamente.. Dessa forma, permite que o tamanho de partículas dos produtos individuais possam ser mudados, alterando as peneiras do moinho. Como desvantagem tem-se um alto custo de investimento em silos e transportadores adicionais e produtos que contenham muita fibra (cevada, aveia, etc.) tornando-se difíceis ou até impossíveis de serem moídos sozinhos.
A pós-moagem em contraste tem a vantagem de menor investimento por necessitar menos silos e elementos de transporte. O produto moído tem uma estrutura mais uniforme pois todos os ingredientes são moídos com a mesma peneira e produtos de difícil moagem quando misturados são mais fáceis de moer. A grande desvantagem da pós-moagem é que ela esta diretamente ligada a linha de mistura e a capacidade da linha dependente da capacidade de moagem. Neste sistema a capacidade do moinho não é completamente utilizada, e o moinho trabalha vazio entre as bateladas.
MOAGEM
No processo de redução de tamanho de partículas, o equipamento mais utilizado mundialmente é o moinho de martelo. Por isso, neste trabalho abordam-se apenas as peculiaridades deste equipamento.
Moagem é mais do que simplesmente o equipamento moinho de martelo, ele é um sistema composto de diversos acessórios, conforme apresentado na Figura 3.
O alimentador (A) e o respectivo controle automático proporcionam a alimentação do moinho, sendo a capacidade de produção ajustada via conversor de freqüência, ligada ao motor do alimentador e limitando a carga pelo uso da potência do motor principal do moinho. Este equipamento deve possuir separador de materiais estranhos e proteção magnética para proteger a integridade da peneira e martelos e minimizar o risco de explosão.
O pulmão funcionará como um plenum que permitirá a redução do arraste de finos, fazendo que a maior parte do produto se direcione para a rosca extratora (I). Muito importante é a existência de sensor de nível máximo para proteger, no caso de ocorrência de anomalia, contra o embuchamento do moinho.
O sistema de aspiração é composto de exaustor (H) e filtro (B), e tem a função de auxiliar na retirada do produto da câmara de moagem.
A clapeta (K) da rosca extratora forma um selo, fazendo com que o fluxo de ar passe apenas pela entrada de ar (D) do moinho, e, através da câmara de moagem, deste modo permitindo a máxima eficiência de moagem.
Para atender proteção contra explosão existem dispositivos adicionais que devem ser instalados, diafragma de ruptura com dispositivo de desligamento (E), que quando da ocorrência da ruptura aciona o fechamento do dispositivo de fechamento rápido (G), evitando a propagação da explosão para a parte interna da fábrica. O duto de alívio (F) direciona a explosão para a parte externa do prédio.
O padrão de medida de tamanho de partícula é o DGM - Diâmetro Geométrico Médio, com a medida de dispersão DPG - Desvio Padrao Geométrico. Para o cálculo destes indicadores recomenda-se a utilização do aplicativo SoftGran disponibilizada pela Embrapa [5].
A seguir, apresenta-se o DGM recomendado por espécie:
Suínos - 500 a 650 μ (mícron)
Aves - 800 a 1.000 μ
Quanto menor o DPG, mais uniforme é a distribuição e melhor será para o desempenho das aves. Segundo o autor Nir [11], o DPG aumenta com o aumento do teor de finos. Existe certa controvérsia quando do uso de granulometria mais grossa para aves, pois tem-se o paradigma de que granulometria grossa afeta a qualidade de pelete. Kleyn [8].cita Reece (1986), onde este mostrou que moagem com peneira de 4,15 mm e 6 mm resultaram respectivamente granulometria de 910 micron e 1024 micron, tiveram qualidade de pelete medida pelo PDI similar de 91%. Este mesmo autor cita a opinião de Penz (2002) que utilizaria milho moído mais grosso mesmo significando menor qualidade de pelete.
Quando a peletização é projetada para a qualidade de pelete, é possível conciliar o tamanho de partícula mais grossa na moagem e adequada qualidade de pelete, entre 80 a 85% de PDI. Este assunto de tamanho de partícula será apresentado novamente no tópico peletização a luz de novos trabalhos.
Fatores que influenciam a moagem
Os fatores que influenciam a moagem são a matéria-prima, a velocidade periférica dos martelos, as características dos martelos e da peneira, e por fim, a ventilação. Matéria Prima: as propriedades de plasticidade e solidez das matérias prima definem o comportamento de moagem.
A seguir, apresenta-se a relação entre as matérias prima e a capacidade de moagem:
Pela relação acima pode-se estimar que um moinho que produz 1 ton/h com aveia, produzirá aproximadamente 4 ton/h com milho.
Outro fator importante na matéria-prima é o teor de umidade do produto, considerando-se que o aumento de umidade de aproximadamente 1%, resulta em aumento de consumo de energia de aproximadamente 7%.
Velocidade Periférica: normalmente a velocidade periférica é de aproximadamente 90 m/s. Se a velocidade periférica for superior a 90 m/s, então a partícula que já estiver no tamanho certo, tem menos tempo para deixar a câmara de moagem, acarretando uma subseqüente redução de tamanho. Com isso, resulta maior proporção de finos, com maior consumo de energia elétrica especifica.
Figura 4. Influência da velocidade periférica sobre o tamanho de partícula Fonte: Kersten [6]
Conclusão: maior velocidade periférica, granulometria mais fina, maior potência e menor capacidade de produção.
Características dos Martelos: a eficiência de moagem está relacionada com o número, a espessura e o desgaste dos martelos.
Quanto maior o número de martelos, maior a probabilidade de que as partículas serão processadas várias vezes gerando uma granulação mais fina. Sendo assim, conclui-se que com menor número de martelos, menor será o consumo de energia e a granulometria do material será mais grossa.
Figura 5. Influencia do numero de martelos sobre o tamanho de partícula Fonte: Kersten [6]
Martelos endurecidos mais finos (3 mm), geralmente afetam positivamente a moagem. A capacidade do moinho é maior, o consumo de energia especifica é menor do que martelos mais grossos (9 mm). Martelo mais grosso empurra o material ao invés de reduzir o tamanho.
Martelos com desgaste exagerado acarretam aquecimento do produto, redução de produção e o risco de rompimento da peneira.
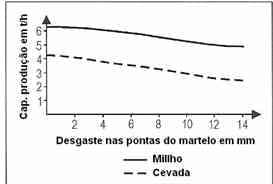
Figura 6. Influência do desgaste do martelo sobre a capacidade de produção Fonte: Kersten [6]
Características da Peneira: a eficiência de moagem está relacionada com a espessura, diâmetro do furo e área aberta da peneira.
Normalmente se usa peneira perfurada com espessura de 2 a 3 mm e com diâmetro do furo de 2,5 a 5 mm. Furos de peneira menor, somente em rações para peixes e pet food.
Quanto maior a área aberta, mais rapidamente as partículas com tamanho adequado deixarão a câmara de moagem. Com isso, resulta em maior capacidade de produção e menor consumo de energia especifico. O efeito colateral negativo de maior área aberta é a maior fragilidade da peneira. O valor de área aberta está entre 30 a 50%.
Figura 8. Influência da área aberta de peneira e umidade do produto sobre a capacidade de produção Fonte: Kersten
Ventilação: o volume de ar fluindo através da câmara de moagem, permite que as partículas com o tamanho já adequado, passem mais facilmente através da peneira. Dessa forma, evita a redução adicional desnecessária da partícula, a formação de finos em excesso e maior desgaste do martelo e da peneira.
Conclusão:
- § Maior capacidade do moinho;
- § Para moagem grossa, o intervalo de granulometria fica mais estreito (menor DPG);
- § Menor consumo de energia especifico;
- § Menor desgaste.
A ventilação afeta o conteúdo de umidade do produto. Dependendo do material e tamanho de partícula desejado, podem acontecer perdas de umidade de até 1%.
Na Tabela 1 apresenta-se resumo dos fatores de moagem de acordo com o SFT -
Swiss Feed Technology Institute
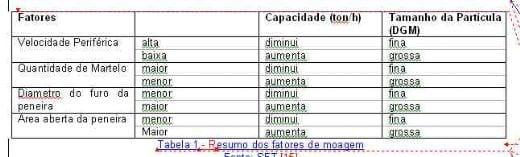
Tabela 1 - Resumo dos fatores de moagem Fonte: SFT
Fatores de Dimensionamento do Sistema de Moagem
Os principais itens que devem ser dimensionados em um sistema de moagem são: capacidade do moinho, volume do pulmão, volume de ar do sistema de aspiração, perda de carga do sistema e tamanho do filtro.
Capacidade do Moinho: depende da potência do motor principal, diâmetro de abertura do furo da peneira e do tipo de material a ser moído (fator jkW).
Q = P x d x JKW
onde:
Q - capacidade de produção (kg/hora)
P - potência do motor principal (w)
d - diâmetro do furo da peneira (mm, intervalo de 2,5 a 7 mm)
JKW - fator da matéria prima
Tabela 2 - Lista jkW de vários produtos usados na industria de rações. Fonte: Adaptado de Ruetsche
Deve ser considerado o jkW de 45 para o milho brasileiro.
Volume do Pulmão: está relacionado com a área da peneira.
volume do pulmão em m3 = m2 da peneira
Volume de ar: podem ser utilizadas as seguintes recomendações para o cálculo:
SFT [16]. recomenda via relação com o tamanho da peneira
Volume de ar em m3/min = Área da peneira em dm2 / 2
Ruetsche [13]. recomenda relação com a produção do moinho
Volume de ar em m3/min = capacidade máxima do moinho em m3/h x 2
Perda de carga do sistema: soma-se as seguintes parcelas:
mm do moinho - 100 a 150 mm de coluna d'água
mm do filtro - 100 a 150 mm de coluna d'água
Recomenda-se um sistema de aspiração individual para cada moinho, quando for utilizado mais de um moinho por linha de produção. O motivo disso é porque cada moinho possui uma perda de carga diferente.
Área das mangas do filtro: está relacionada com o volume de ar de aspiração.
Usar a relação de 4 m3/min de volume de ar / m2 de área de filtro.
As referências apresentadas anteriormente servem como base e dão uma idéia de grandeza, sendo que cada fabricante de equipamento pode em maior ou menor grau otimizar certos parâmetros da máquina permitindo uma melhor eficiência.
Operação
Para manter a melhor eficiência da moagem deve ser criada uma rotina operacional de inspeção que atenda pelo menos os seguintes pontos:
- retirada dos materiais estranhos;
- reversão da rotação;
- controle de desgaste dos martelos;
- controle de desgaste das peneiras;
- controle da perda de carga do filtro e limpeza das mangas.
REFERÊNCIA BIBLIOGRÁFICA
[1] Amerah, A.M.,Ravindran,V., Lentle,R.G. and Thomas, D.G. Influence of Feed Particle Size and Feed Form on the Performance, Energy Utilization, Digestive Tract Development, and Digesta Parameters of Broiler Starters. Poultry Science, 2007, Vol. 86, No. 12, pp. 2615-2623, 33 ref.
[2] Amerah, A.M.,Ravindran, V., Lentle, R.G. and Thomas,D.G. Influence of Feed Particle Size on the Performance, Energy Utilization, Digestive Tract Development, and Digesta Parameters of Broiler Starters Fed Wheat- and Corn-Based Diets, Poult. Sci., November 1, 2008; 87(11): 2320 - 2328.
[3] Briggs,J.L., Maier,D.E., Watkins, B.A., Behnke,K.C.. Effect of Ingredients and Processing Parameters on Pellet Quality. 1999 Poultry Science 78:1464-1471.
[4] Buhler, notas técnicas 2009.
[6] Kersten, J.,Rohde, H. Nef, E. Principles of Mixed Feed Production - Components . Processes . Technology, 2005.
[7] Klein, A. Peletização de Rações Aspectos Técnicos, Custo e Benefício e Inovações Tecnolólicas. Conferência FACTA 2009 de Ciência e Tecnologia Avícola 21º Congresso Brasileiro de Avicultura.
[8] Kleyn,R. The Effect of Particle Size on Poultry Performance, SPESFEED (Pty) Ltd
[9] Lara, M. Mistura em Fábricas de Rações. SAPIA - Sistema de Aperfeiçoamento da Industria de Alimentos. Módulo: Equipamentos de alimentos para animais. Paulínia 3 a 4 setembro de 2003.
[11] Nir, I., Pitichi,I., Feed Particle Size and Hardness: Influence on Performance, Nutritional, Behaivioral and Metabolic Aspects - Advances in Nutritional Technology 2001, Utrecht.
[12] Payne, J.D. Troubleshoting the Pelleting Process. Feed Technology. Technical Report. American Soybean Association. International Marketing Southeast Asia.
www.asasea.com[13] Ruetsche, P., The Progressive Animal Feed Production and its Fudamentals 1 - Griding / Sieving in the Feed Milling Industry. Advances in Feed Technology No.1, Verlag Moritz Schäfer. 1989.
[14] Robohm,K-F. The Influence of Gap Width Adjustment between a Feed Pellet Mill's Roller and Die on Throughput, Energy Demand and Pellet Quality. Advances in Feed Technology No.3, Verlag Moritz Schäfer. 1990.
[16] SFT - Swiss Feed Technology Institute, notas do curso 1996, Uzwill, Suiça.